Aluminium Hard and Semi-Hard Anodizing
(thicknesses from 25 to 150 microns)
The hard anodizing treatments are addressed to those parts, generally intended for industrial use, that have high precision and reliability objectives. In fact, with the hard anodizing, we give to the parts characteristics of high surface hardness, as well as corrosion and frictional resistance, thermal and chemical resistance. For these reasons, the aluminium hard anodizing is a widely used treatment in several fields, from mechanical to motorcycle and automotive, from textiles to military and aeronautics.

Aluminium hard anodic oxidation treatments
The standard treatment does not provide any colouring, therefore the final aesthetic aspect of the part will vary in reaction to the alloy used and the required thickness standard. If Ergal alloy (Al 7000 alloy) is used, the finish will range from gilded bronze to dark bronze; for Anticorodal alloys (Al 6000 alloy) the final result will go from a pearly grey to anthracite or with a green cast. Peraluman alloys (Al 5000 alloy) result in shades of grey. This depends on the different reaction of the chemical compositions to the alloys. With regard to the possibilities of application of hard anodizing, it is made on all aluminium alloys with Cu <2.5% and reaches a thickness of 25 to 150 microns.
Other aluminium HARD anodic oxidation treatments
With the hard anodic oxidation treatment is possible to improve the resistance of the aluminium alloys surfaces. In addition to this type of process, New Oxidal also offers other hard oxidation treatments for aluminium, among which:
Hard colour anodizing: in the phases of the hard anodizing treatment, the aluminium part is subjected to colouring based on organic pigments. In this way, the part, in addition to having all its functional characteristics, is also appreciable from an aesthetic point of view;
Hard oxidation with PTFE impregnation: if the part must have non-stick and smooth characteristics, the PTFE impregnation treatment follows the hard anodizing treatment. The non-stick PTFE polymer is incorporated in the anodic layer thus ensuring low friction coefficient and low wettability. It is the ideal process for the parts used in sliding, friction, in contact with ferrous materials, with liquid components or with high adhesiveness such as glues, paints, etc. The PTFE impregnation can also follow the hard coloured anodizing treatment.
Semi-hard oxidation with natural and pigmented thickness: the applications of this treatment are very wide since, while maintaining high characteristics of resistance to corrosion and contact, it significantly lowers the microfracture point of the anode layer. The anodic layer, more flexible, has greater resistance when supported by torsion or tension stress. By resorting to semi-hard pigmented oxidation, the material also ensures great aesthetic quality. The thicknesses normally reached range from 20 to 50 microns.

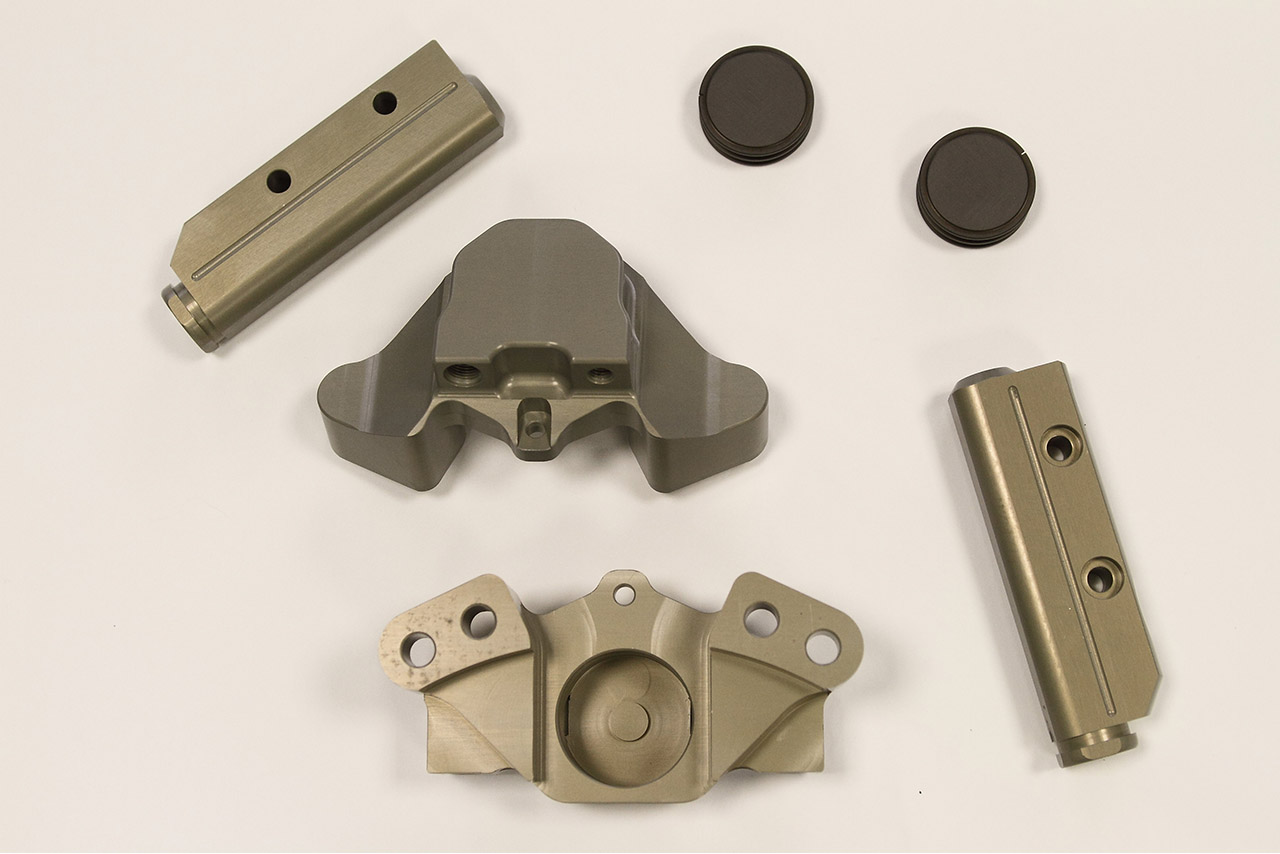
Aluminium Hard and Semi-Hard Anodizing: why contact New Oxidal?
New Oxidal in Brescia carries out aluminium hard and semi-hard anodizing treatments based on customer specifications and in compliance with the ISO 10074:2017, UNI 7796:2010 and MIL-A-8625F type III class 1 and 2 standards, offering the following advantages:
High corrosion resistance;
Maximum thermal and chemical resistance;;
High resistance to wear and friction;;
Versatility of use(thickness from 20 to 150 microns, surface hardness from 350 to 1000 HV);